Project Overview
This case study seeks to deploy AUSMOS in an unknown environment to perform mapping where qualitative assessment may be made to ground landmarks (e.g. open pit) and existing utility maps. ULC Technologies’ operatives deployed AUSMOS on two adjacent sites at Clapham Hill, London UK, where it successfully completed an operation from scanning through to interpretation and mark-out. This autonomous mapping took place in a semi-congested region as traffic continued flowing with minimal disruption to local residents. While abiding by regional traffic management guidelines, AUSMOS mapped out a 25 square meter region within a few hours.
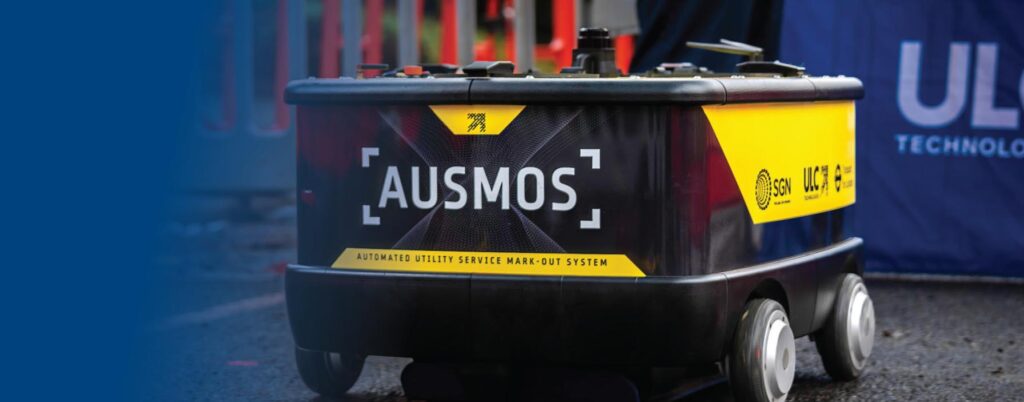
Location: London, UK
Site 1 Region Size: 5.5m x 2.3m
Site 2 Region Size: 3.1m x 3.9
Background
Ground penetrating radar (GPR) has the ability to penetrate the ground and measure both the electrical properties of the subsurface as well as other physical characteristics such as stone/rock composition. It can also be used for a variety of applications including identifying the location of buried objects and mapping underground utilities. However, GPR is still not used as widely as it should be today in the industry. This is due to the GPR processing method being very time-consuming and technically challenging because of the precise adjustments that must be made in order to collect accurate results. Errors from human or machine sources must be manually identified and corrected before detailed analysis can begin. In addition, due to its complexities, GPR data processing and interpretation has traditionally taken place off-site. This process can introduce significant delays to projects.
AUSMOS is a semi-autonomous robotic platform that detects and marks-out belowground infrastructure utilizing a sensor suite comprised of ground penetrating radar and electromagnetic sensors. This robotic platform automates underground mapping enabling denser GPR data collection and more powerful post-processing techniques that results in easier to interpret data, reducing the risk for accidental damage to buried assets. AUSMOS can provide a variety of benefits when collecting and mapping underground assets compared to traditional methods, including:
- Same day data collection, processing and road mark out
- Higher density and higher resolution data
- No human bias/error in data collection
- Accurate localization in GPS denied environment
- Fully autonomous and simple deployment
Case Study: Clapham Hill, London
This case study seeks to deploy AUSMOS in an unknown environment to perform mapping where qualitative assessment may be made to ground landmarks (e.g. open pit) and existing utility maps. ULC’s operatives deployed AUSMOS on two adjacent sites at Clapham Hill, London UK, where it successfully completed an operation from scanning through to interpretation and mark-out. This autonomous mapping took place in a semi-congested region as traffic continued flowing with minimal disruption to local residents. While abiding by regional traffic management guidelines, AUSMOS mapped out a 25m2 region within a few hours. This mapping process took place in an urban environment in southwest London where GPS signal can be sporadic. As AUSMOS’ localization is GPS agnostic, its results were not impacted.
At Clapham, ULC identified two sites for mapping- these regions are shown in the figure below. For these scans, ULC’s team requested the utility maps from the respective owners and was used for qualitative analysis. These maps are shown below.
Picture above: Scanning regions of interest and utility survey of regions of interest
At each respective site, ULC’s team deployed AUSMOS using its ground penetrating radar and electromagnetic sensors. During these tests, all processing was done on-site by ULC’s team of two, without evaluation by a subject matter expert. This interpretation was performed through AUSMOS’ user interface where both three dimensional and two dimensional results are shown. An example is shown in the accompanying figure from AUSMOS’ site 1 scan. Following processing, indications of assets were marked-out by the operators using the robot. These results are also included below.
Following mark-out ULC’s team captured drone images that could be used for qualitative analysis of the results. The analysis was focused on three main areas of interest:
- Agreement with existing utility drawings
- AUSMOS’ mark-outs in correspondence to the existing pit on site
- The correspondence of mark-outs in adjacent areas and their localization relative to each other
Firstly, results were evaluated in the context of the available utility drawings. Site 1 identified three potential assets, but these mark outs do not include that of the exposed 24” pipe. This was expected because the robot did not capture data on the walkway at site 1, and as a result, did not cross over the asset in question. However, since site 2 crossed over the region, this pipe became visible in the second scan area. Of the assets captured in site two, one asset should be expected to be the 24” cast iron gas main, and the others may include the water/trunk mains.
In addition, its worth noting that data acquisition was performed in a single antenna orientation for both tests. Where traditional GPR systems map utilities using grid scanning techniques, AUSMOS’ post-processing is more agnostic to the antenna orientation during data collection. This post-processing allows for its system to capture and reconstruct data in more generalized orientations more effectively than traditional GPR processing algorithms.
Pictures above: Site 1 (left) and Site 2 (right) same-day mark-out performed by AUSMOS at Clapham.
The second area of interest was related to the mark-outs correspondence to existing infrastructure, in this case the pit. To evaluate the relative accuracy of the mark-outs, the drone images were used to project the potential path of the 24” gas main. These results were then qualitatively compared to markings made by AUSMOS which showed strong correspondence. This comparison is shown in the figure below and shows the accuracy of the localization of the robot in urban environments.
Picture above: Projection of paint marks to exposed pit and correspondence to AUSMOS mark-out. The white line shows the projected path of the 24” gas main into site 2. The yellow lines highlight the actual line marked out by AUSMOS.
The final evaluation herein includes the that of comparison between both independently mapped regions. In this case, the focus is paid to do potential assets that appear in adjacent regions reflect mark outs that are in agreement. This test seeks to understand the robot’s repeatability of measurement. To make this assessment, the drone image is used to draw projected mark-outs from site 1 into site 2. The results show that these mark outs agree with each other highlighting the repeatability of the processes.
Picture above: Comparison of paint marks in two adjacent regions that were scanned and marked out independently of each other. The white arrow shows the projection of mark-outs from site 1 into site 2. The yellow arrows highlight the paint markers placed at site 2.
Overall, this case study highlights AUSMOS’ potential for use in urban environments where there is likelihood of congested utilities buried. AUSMOS’ team of two were able to map approximately 25 square meters in a few hours. These markings not only showed strong correspondence to the open pit on site, but also provided strong correspondence to each other.
This testing performed all operations from data acquisition through road mark-out on the same day without analysis from a subject matter expert. This was made possible by AUSMOS’ denser data collection which resulted in higher resolution data and subsequently a higher confidence map.
ULC Technologies is continuing with the deployment of the robot both in the UK and US. This will focus on demonstrating the AUSMOS technology across various use-cases. If you are interested in learning more about AUSMOS or discussing a pilot program, please contact our team.