Project Overview
ULC Technologies developed the Air Gap Inspector for ABB, a leading engineering company, to provide inspection services for large motors and generators around the globe. With our client’s expertise in engineering, constructing, deploying, and servicing motors and generators and ULC’s expertise in robotic systems development, the robotic crawler was successfully developed and piloted and is now being used to service customers on a regular basis.
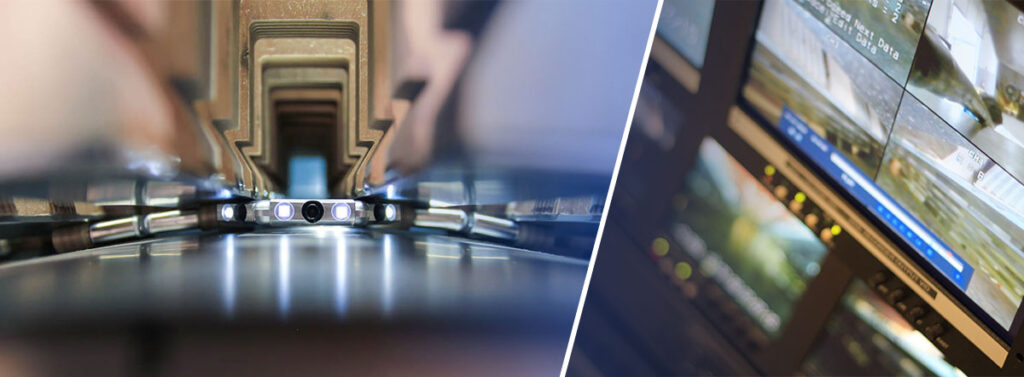
Client: ABB
Project Date: Completion – June 2017
Other Benefits:
The data gathered provides a more efficient method to inspect the machines in depth by also identifying:
- Broken laminations
- Core burns
- Blocked vent ducts
- Effects of spark erosion and bulging
- Signs of movement at slot exit or in vent ducts
Project
ABB, a leading global engineering company, approached ULC Technologies to design and build a crawler robot for inspecting the air gap (the gap between the stator and rotor) of large motors and generators. The client and ULC worked collaboratively to develop a robotic crawler system capable of entering air gaps as small as 10mm to provide video depicting the condition of the stator and rotor. The crawler provides video and accurate location of problem areas which supersedes any of the standard methods for inspections. The research, development, and manufacturing of the Air Gap Inspector by ULC allows the engineering firm to generate information that can better inform owners of the longevity of their assets and allow them to make decisions whether and when to repair or replace components.
Proof Of Concept Through Production
ULC and ABB partnered on a phased approach for the research and development of the robotic system.
Beginning with an early proof of concept, ULC Technologies performed conceptual design and early prototyping to test theories and concepts for the system. After just one year, the proof of concept crawler was successfully tested in a mock generator environment and validated by the engineering firm. Through continuous improvements, the product was refined and field tested in various motors and generators worldwide.
As the manufacturers of the Air Gap Inspector, ULC Technologies sourced, custom-built, assembled, and tested the robot with its micro-sized components. And by working closely with the client, the crawler system was completed from precisely machined parts, motors, cameras gears, bearings, and electronics to ensure the system was operating efficiently in the confined 10mm space.
Results
- All crawlers are assembled and 100% functionally tested at ULC’s Hauppauge facility
- Our engineering team manufactured several complete Air Gap Inspector Systems including spare parts and tools for deployment and upkeep
- ULC designed and hosted an intensive training program for the client’s technicians who are now deploying the Air Gap Inspector Systems globally
- ULC supports ABB in providing technology deployment services to ABB’s customers in the U.S. while the client services the customers in other countries around the globe.