Project Overview
Gas main rehabilitation projects are highly complex and require detailed project planning and preparations to deliver projects on time and on budget. Pre-inspection of the live gas main in the early planning stage can now be conducted to identify all the unknown conditions so the gas utility can more accurately estimate project costs and improve go/no-go decision making without disrupting gas service to customers.
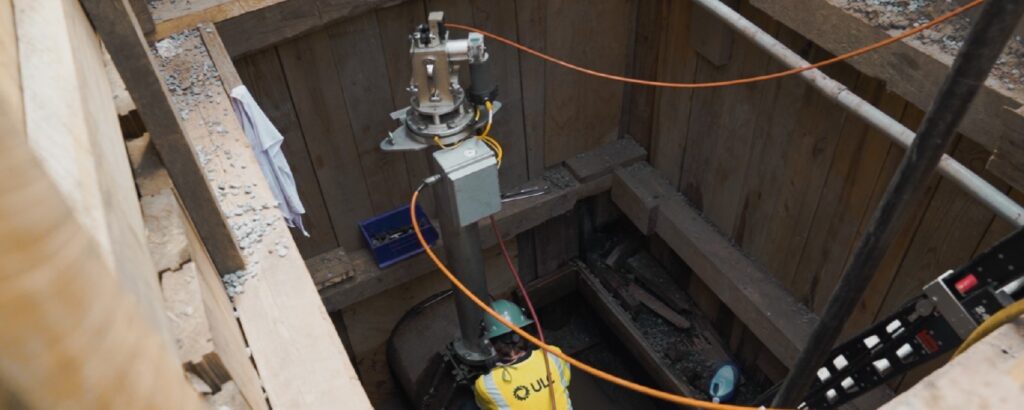
Industry: Gas Distribution
Client: PSE&G
Location: South Orange, NJ
Gas Main: 30″ Cast Iron Low Pressure
Points of Entry: 1
Total Inspection Distance: 355ft
Business Areas Addressed:
- Pre-Rehabilitation Inspections
Results:
- High-quality imagery and valuable mapping data provided
- Better planning and informed decision making from data gathered
- Improved project efficiency
Background
When the time comes to replace large diameter gas distributions mains, many gas utilities choose to rehabilitate the pipeline instead of directly replacing the pipe. Trenchless technology, such as CISBOT, lining, and insertion help gas utilities lower costs while minimizing disruption to the public and environment. These renewal projects are also delivered much faster than traditional replacement, translating to less time in the street.
Unknown conditions in the pipe can complicate gas main rehabilitation projects—increasing budgets and timeframe—but these conditions are often not known until after the utility has shut down the pipe and dug numerous excavations. In many cases, the utility has no choice but to move forward with the project as they have already invested a significant effort and investment into the project.
“We are using live CCTV to verify the geometry of the pipe, identify any anomalies and determine cleaning requirements in preparation for lining as a renewal technique at this location.”
George Ragula, Distribution Technology Manager, PSE&G
30″ Gas Main Pre-Lining Inspection – PSE&G, South Orange, NJ
PSE&G is the largest provider of electric and natural gas in New Jersey, serving 2.3 million electric customers and 1.9 million gas customers. In South Orange, NJ a leaking condition on a 30” cast iron gas main prompted the need to address the pipeline. Located under a busy commercial street, the utility opted to renew the pipe using lining to avoid the costs and disruption associated with pipeline replacement.
Unknown conditions in the pipe may:
- Interfere with the rehabilitation process
- Increase project duration and costs
- Require emergency repairs to be done to the pipe
- Damage the liner during the installation process
George Ragula, Distribution Technology Manager at PSE&G, contacted ULC Robotics to conduct a live CCTV inspection to verify features in the pipe and identify anomalies in preparation for gas main rehabilitation. The utility specifically wanted to see a reducer that transitioned the pipe from a 30” to a 36” in addition to back-to-back 45° bends.
Inspection & Results
To conduct the pre-lining inspection of the 30” cast iron main, ULC Robotics utilized the Large VGC Live Gas Main Inspection Crawler System. The tethered pipeline crawler system is designed to enter the gas main through a specialized launch tube and travel hundreds of feet in either direction from the point of entry to conduct a visual inspection of the pipeline and features visible from within the gas main.
In preparation for the live gas main pre-rehabilitation inspection, the utility identified an optimal entry point, created an excavation, and provided a 4” tap through a valve under no-blow conditions. The valve acts as an entry point for ULC’s Large VGC Live Gas Main Inspection Crawler System.
Once the Large VGC enters the gas main, the crawler expands to allow the tracks to ride on the sides of the pipe. This provides an optimal point of view for ULC’s operators to conduct the inspection, allows the crawler to navigate past debris commonly found at the bottom of the pipe, and enables further travel distances.
Within one day, ULC’s crews inspected the gas main in both directions to deliver high-quality imagery and valuable mapping data so PSE&G and their contractor can plan the lining project and make more informed decisions. Data provided by the inspection helped confirm that the pipeline was suitable for lining. No anomalies were identified, and the geometry of the pipeline was confirmed. Also, all the work was done without interruption of gas service to the customer so PSE&G could avoid disrupting customers and having to invest in purging the main.