Project Overview
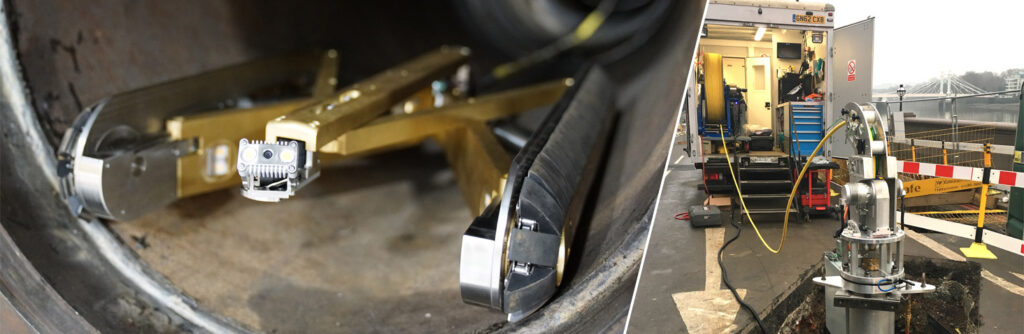
Industry: Gas Distribution
Client: tRIIO, Cadent
Locations:
- Chelsea Embankment and Battersea Bridge
- St. Leonards Rd., London
- Brompton Rd., Knightsbridge
Results:
- Successful field trial of new technology
- Reduced the number of excavations required during enablement works
- Improved ability for gas network and contractors to plan projects
- Minimised impact on the public and environment
Project Description
The project required pre-inspection of the mains using a robotic inspection crawler to accurately map the buried infrastructure and plan the project, but internal seals prevented the use of crawlers.
In a strategic alliance developed between ULC Technologies, tRIIO, and Cadent, with support provided by Transport for London’s Lane Rental Funding, new technology was developed to expand gas network internal inspection capabilities in large diameter mains and enable inspection in mains not previously accessible by existing technologies.
Challenges
Existing pipeline inspections systems were unable to survey a majority of the London gas distribution network due to pitfalls due to the historic installation of internal seals.
- Internal mechanical seals prevented crawlers from traversing the gas main.
- The location of internal seals were not well documented, making it near impossible to know which sections of the main had been repaired with these seals.
“Utility networks often reverted to the excavation of trial holes for inspection purposes. The excavations not only required extra manpower, but induced further delays, congestion, and costs to all associated parties.”
Solution and Results
Following an intensive research and development period, the M1 Live Gas Main Inspection Crawler System was deployed at three locations within the London Medium Pressure network.
- The no-blow launching system was adapted to a bond and bolt style fitting to further reduce excavation, disruption and costs
- Successful passage through 677m of large diameter gas main containing 220 internal mechanical seals, eight 11.5° bends and two 22.5° bends
- Eliminated the need for numerous street excavations to reduce the impact on drivers, cause less congestion, and lower overall project emissions
- All works were carried out under live gas conditions–eliminating the need to reduce pressure in the mains or shut off gas for customers
Reports generated by ULC field technicians during the surveys detailed the location of all internal seals, bends, and other features, allowing Cadent and tRIIO to complete the essential work quickly and with minimal inconvenience to the people who live, work, and travel through the area.