Project Overview
To improve cross bore safety for new gas main and gas service installation projects, PG&E collaborated with ULC Technologies to deploy a new acoustic cross bore detection method on gas distribution facilities that were just installed.
The X-ID® sensor was deployed over a period of two-days where the technology cleared several gas service installations and 645 ft of gas main installations with a primary goal of understanding how this technology integrates with gas construction crews. In addition to verifying no damages were created from the trenchless installation project, X-ID® proved to have little to no impact on construction schedules. Additionally, the efficiency of inspections indicated that X-ID® could drastically reduce inspection timeframes to lower cross bore risk in the gas network.
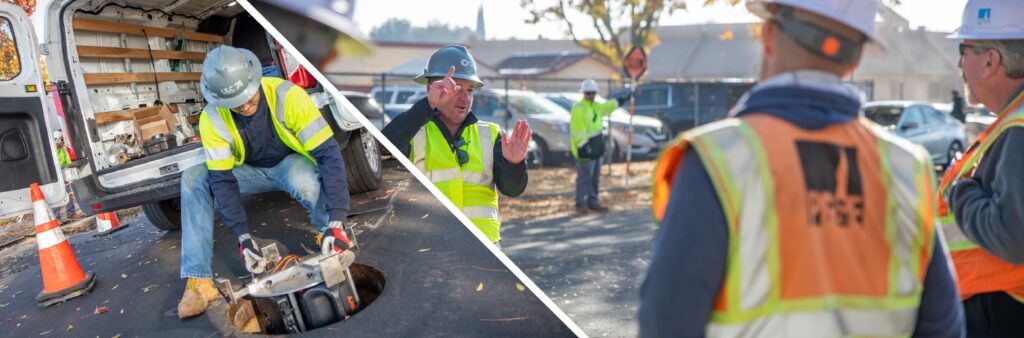
CLIENT:
PG&E
LOCATION:
Waterford, CA and Modesto, CA
PROJECT STATS:
• Several gas service installations inspected with X-ID
• Two gas mains installations inspected with X-ID
RESULTS:
• No cross bores detected
• Successfully proved new inspection process had little to no impact on construction schedules
• Lowered cross bore risk before tying in new mains and services
SOLUTION OVERVIEW
ULC Technologies, in close collaboration with our utility partners, has developed a patent-pending acoustic inspection system to detect and locate cross bores that address cross bore safety – X-ID®. The method consists of introducing a unique sound pattern into sewer mains and laterals, via manholes and P-traps, and detecting the sound pattern from within the gas pipe.
The existence of a cross bore will cause the sound to propagate from the sewer pipe into the gas pipe. If the sound pattern is detected in the gas pipe, any position along the gas pipe exhibiting a peak in the sound level is identified as a potential cross bore.
This acoustic technology allows for much higher daily production rates and is expected to significantly decrease or eliminate the risk of “uninspected” locations where conventional inspection methods could not keep up with the demand.
DAY 1: NEW GAS SERVICE INSTALLATION
The first day of the pilot focused on inspecting multiple gas services that were installed using horizontal directional drilling the previous day in Waterford, CA. The 1” PE services were not yet tied into the main or connected to the customer’s meter and were between 35 and 93ft in length.
As with all projects, the X-ID® acoustic transmitters were installed under the sewer manhole covers so the dynamic acoustic signal can travel throughout all the sewer main piping and all service lateral piping. A pre-inspection speaker check and pre-inspection sensor check were performed as part of written procedures. These checks are mandatory prior to inspection to verify the sensor functionality and confirmation of signal travel throughout the entire sewer main system.
Over the course of the day, the X-ID® system inspected several gas services which exceeded the expected productivity. Multiple gas services were accessible from existing excavations in the street so the ULC inspection crew could inspect multiple services from one setup location. This configuration led to higher-than-expected production rates and efficiencies.
During this project ,the X-ID® did not detect any cross bores since none were present at this location, but ULC and PG&E proved out the lack of disruption to the installation process and ability to quickly perform cross bore inspections immediately after HDD installation. Quick turnaround on post HDD inspections can eliminate the risk associated with uninspected gas mains and services post tie-in.
“Sewer-based cross bore inspections are limited by what they can see and access,” says Nate Naylor, Superintendent at PG&E. “This acoustic process can pinpoint a cross bore even if it is covered in water or debris. Additionally, it can identify near-miss locations to help support QA/QC and inform where training needs to improve.”
DAY 2: NEW GAS MAIN INSTALLATION
The second day of the technology deployment focused on supporting post-HDD gas main cross bore inspections. The inspection was conducted following the trenchless installation of a 400ft and 245ft length of 2” PE in Modesto, CA. At the time of the X-ID® project, the 2” main was not tied in and open ends of the pipe were accessible from the excavations on either end of the main.
ULC’s field technicians installed the X-ID® acoustic transmitters in adjacent manhole locations to ensure the signal sufficiently covers the sewer and any laterals. Manhole covers were able to be re-installed over the speaker to re-open the street to traffic during the pilot project.
The pre-inspection speaker check and pre-inspection sensor check was performed to verify the sensor functionality and confirmation of signal travel throughout the entire sewer main system.
Working from just one excavation, ULC’s field team was able to access both lengths of the gas main. Since the X-ID® operation did not require any contractor support, the ULC crews were able to inspect the newly installed gas main directly after the HDD installation as the installation contractor crews were drilling at the next location to eliminate any disruption to construction schedules.
The inspection of both mains was completed within a single day with no additional excavations or pipe work required. While no cross bores were detected at this project location, ULC and PG&E were able to demonstrate that deployment of X-ID® had no impact on contractor crews and enabled rapid post-HDD cross bore inspection.
X-ID®: Key Takeaways for New Installation Cross Bore Inspections
The two-day X-ID® deployment at PG&E was focused on using acoustic cross bore detection technology to improve the post-HDD inspection process. Most utilities that use HDD installation methods for gas mains and services are required to perform a post-construction inspection to ensure that a cross bore does not exist.
Sewer inspection, which is the current industry standard method of conducting these inspections, is both challenging and costly for utilities – diminishing the cost-saving provided by trenchless construction. For gas distribution utilities, conducting these inspections from within the gas main or service offers a range of benefits:
No Additional Excavations Needed: For new installation projects, X-ID® did not require any additional excavations to launch into the gas mains or services.
Minimal Impact on Contractor Schedules: Work was able to be planned so that inspection can be done after installation and before gas assets were tied in with little to no impact on construction schedules.
Cleaner and Easier Inspection Environment: X-ID® takes the inspections out of the sewers and into the gas pipeline, which is cleaner and easier to access. This also eliminates the need to clean sewers for CCTV inspection.
Better Coverage: Sewers have common issues such as root intrusion, branching and excessive debris, which can result in as much as 15-20% of laterals to be inaccessible. The acoustic signal infiltrating the sewers and laterals can make it past these obstacles so inspections can be completed.
Rapid Inspections: Inspections were able to be completed while contractor crews were still on site before gas is introduced into the pipelines. Had a cross bore been detected, contractor resources on site could have remediated the issue quickly.
Reduce Traffic Control Requirements: X-ID technology lessened the amount of traffic control needed on projects compared to sewer camera inspections—which will deliver a significant cost reduction and minimize disruption to the community.
“ULC Technologies is working with industry-leading HDD contractors to define processes that minimize impact on construction schedules and stay ahead of demand,” says Ryan McGowan, VP of Operations at ULC Technologies. “Our goal is to support large-scale projects across the country and help reduce legacy program backlogs and left-behinds.”
To learn more about the X-ID® Cross Bore Detection technology or to discuss a demonstration, visit our web page or contact us.