Unmanned Rapid
Airfield Damage Repair
Home > Technologies > Rapid Airfield Damage Repair
Technologies
Improved Soldier Safety with Autonomous Airfield Damage Repair
The unpredictable nature of humanitarian and wartime response/recovery requires military operations to rapidly adapt to unforeseen challenges. Traditional airfield damage repair methods require several construction vehicles, as well as multiple highly skilled, cross-trained teams to operate them. Deploying and maintaining such large, specialized equipment can be challenging and costly, especially in austere and remote areas.
ULC Technologies has developed an Unmanned Rapid Airfield Damage Repair (UM-RADR) platform, capable of performing autonomous airfield damage repair advanced repair material. This tracked robotic solution will improve airfield personnel safety and increase repair operation efficiency overall.
In accordance with DFARS 212.70, the UM-RADR concept qualifies for Commercial Solution Opening (CSO) status and is eligible to proceed into contracting with interested DoD partners.
Key Benefits
Enhanced Safety
Increased Efficiency
The deployment of robotics reduces the operational footprint, enhancing agile combat capabilities with less equipment and personnel on-site.
Reliability
RADR provides predictable and reliable operation 24/7, even through extreme weather conditions.
Remote Management
This system offers multi-level remote management and monitoring of repair operations.
Workflow Integration
RADR can be easily integrated with existing UAV surveillance operations, enabling a fully automated workflow.
Rapid Airfield Damage Repair
How It Works
Once the damage assessment is completed (through UAS solutions or survey) the UM-RADR system autonomously navigates past any obstacles to the programmed coordinates of the designated spalls and performs a volumetric assessment of the spall size before beginning the autonomous refill and repair operation. The figures below depict each step in the refill and repair operation:
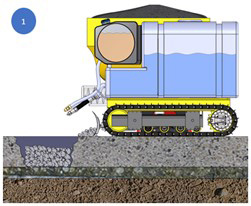
Step 1:
Debris is pushed into the spall
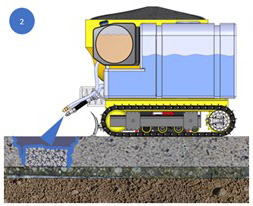
Step 2:
The spall is then coated with water
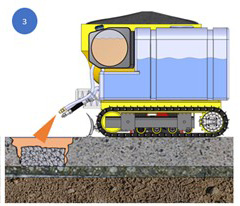
Step 3:
RADR then applies advanced repair material to the spall
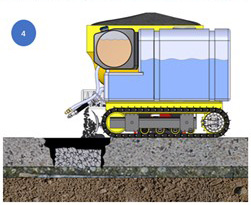
Step 4:
Apply 2-inch lift with local aggregate
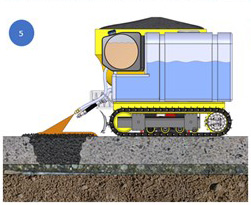
Step 5:
Second round of advanced repair material is then applied
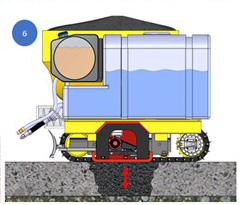
Step 6:
Lastly, tamp area and allow to cure
Leading Innovation. Driving Results.
ULC Technologies develops and deploys robotic systems, smart artificial intelligence processes, and innovative inspection technology for the energy, utility, renewables and industrial sectors.
Talk to our team today: