- Why ULC?
- R&D Services
Research & Development
Leading Innovation. Driving Results.
- Industries
X-ID CROSS BORE DETECTION SERVICES
Our patented acoustic technology detects cross bores from within gas mains and services. Learn MoreLIVE GAS MAIN INSPECTION
We are leaders in the deployment of camera and crawler systems into live gas mains. Learn More
PORTABLE EMISSIONS RECOVERY
Our drawdown compressor technology helps gas distribution utilities reduce emissions. Learn More
AIM: AI-POWERED UTILITY MAPPING
Using vehicle-mounted cameras along with AI and Machine Learning to map electric distribution poles and pole-mounted assets. Learn More
CIRCUIT BREAKER RACKING ROBOT
Breaker Racking RobotAutonomous mobile robot designed to rack and unrack large breakers within substations. Learn More
ELECTRIC CONDUIT INSPECTION
Our field service teams provide video inspection of conduits prior to cable pulls to identify obstructions and pinpoint damages. Learn More
Machine Learning for Jacket Foundation Inspection
ULC used machine learning to enable more efficient inspection of jacket foundations at the Block Island Wind Farm. Learn More
Electrical Conduit Inspection Services
Our field teams provide internal inspection of conduits to pinpoint obstruction and damage prior to cable pulls. Learn More
Robotics & Technology Development
We work with leading energy companies to develop, commercialize, and deploy robotic systems and technologies that support the construction, maintenance, and inspection of infrastructure. Learn More
ROBOTIC GPR MAPPING AND MARK OUT
AUSMOS is an autonomous robotic platform that detects and marks-out below-ground infrastructure using sensors. Learn More
VEST: VACUUM EXCAVATION SOFT TOUCH
VEST improves the performance of vacuum excavation by integrating supersonic air nozzles into the vac-ex tool head. Learn More
UM-RADR: UNMANNED RAPID AIRFIELD DAMAGE REPAIR
Robotic platform is deployed to damaged airfields to remotely perform repairs. UM-RADR qualifies for Commercial Solution Opening (CSO) status. Learn More
- Products & Services
Field Services
Products
Live Gas Main Inspection Cameras
Emissions Recovery
- Company
Project Overview
ULC Technologies’ operatives deployed AUSMOS in the greater London area as part of a greater pilot program. This region was selected due to its highly complex layout including multiple facility types, depths and sizes. This field test was performed by two ULC operatives with limited GPR experience. Following autonomous scanning process, this team was able to deliver post-processed data onsite and used the AUSMOS robot to mark the ground accordingly. Where most utility locating GPR antennas capture data in >25 cm segments in a grid pattern, AUSMOS captured data in 10cm segments in a single scan direction.
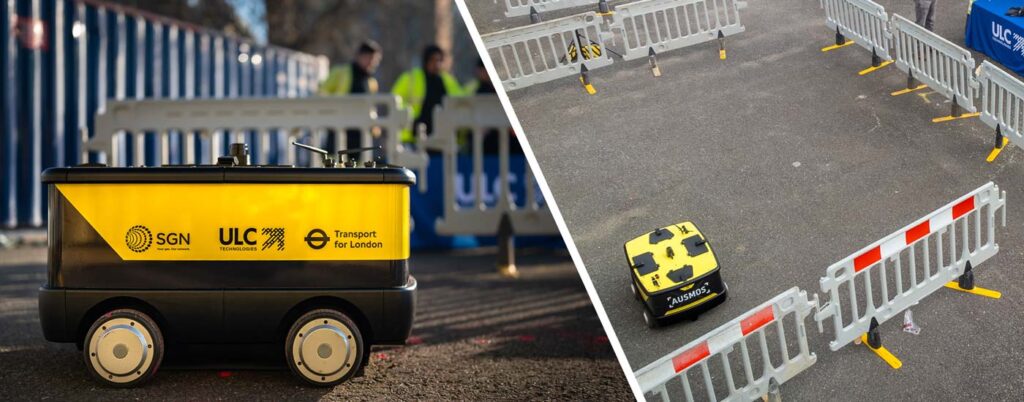
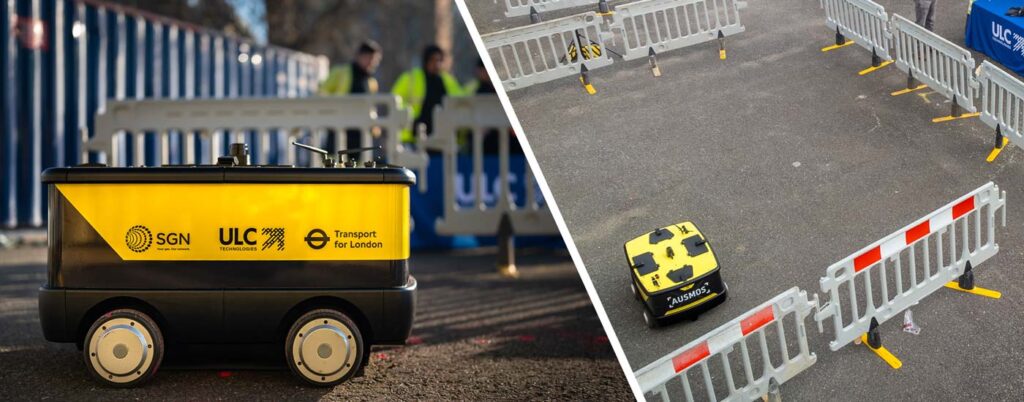
Location: Epsom, UK
Region Size: 3m x 5m
Background
Ground penetrating radar (GPR), while a powerful tool that is capable of capturing both cables and pipes, is often limited in its deployment for utility locating due to complexities in interpreting the raw data. As a result, this interpretation process is often performed offsite by skilled subject matter experts (SME) with extensive background knowledge in geophysics contributing added cost and delays to projects.
AUSMOS, or the Automated Utility Service Mark-Out System, is a is a semiautonomous robotic platform that detects and marks-out below-ground infrastructure utilizing a sensor suite comprised of ground penetrating radar and electromagnetic sensors. This robotic platform automates underground mapping enabling denser GPR data collection and more powerful post-processing techniques that results in easier to interpret data, reducing the risk for accidental damage to buried assets. Using its custom user interface (UI), the robot can provide both three-dimensional point clouds and two-dimensional C-scans to enable operators to identify potential assets more effectively than traditional systems.
AUSMOS can provide a variety of benefits when collecting and mapping underground assets compared to traditional methods, including:
- Same day data collection, processing and road mark out
- Higher density and higher resolution data
- No human bias/error in data collection
- Accurate localization in GPS denied environment
- Fully autonomous and simple deployment
Case Study: Epsom, UK
This case study seeks to deploy AUSMOS to an unknown location where utilities may be mapped by a ULC team without use of a subject matter expert for data analysis. Data is interpreted onsite by ULC’s staff using AUSMOS’s post-processed data alone (no raw data considered). Data is later qualitatively compared to road features (e.g., trenches) and utility maps from the respective facility owner. Its results were not impacted.
ULC’s operatives deployed AUSMOS in Epsom, a town in the greater London area. This region was selected due to its highly complex layout including multiple facility types, depths and sizes. Following scanning, utility maps were obtained where they were used for qualitative assessment to ground marking placed by AUSMOS.
This test was performed by two ULC operatives with limited GPR experience. Following scanning, this team interpreted AUSMOS’s post-processed data onsite and marked the ground accordingly, without any analysis by a third-party subject matter expert. This interpretation was performed using AUSMOS’s UI which provides powerful two and three-dimensional visualization of the buried utilities. Following mark-out, ULC’s team captured drone images which could later be used for comparison to the road surface and utility maps.
Picture above: Utility survey of region of interest
The second area of interest was related to the mark-outs correspondence to existing infrastructure, in this case the pit. To evaluate the relative accuracy of the mark-outs, the drone images were used to project the potential path of the 24” gas main. These results were then qualitatively compared to markings made by AUSMOS which showed strong correspondence. This comparison is shown in the figure below and shows the accuracy of the localization of the robot in urban environments.
The end-to-end robotic GPR scanning operation was completed by two operators. Where most utility locating GPR antennas capture data in > 25 cm segments in a grid pattern, AUSMOS captured data in 10cm segments in a single scan direction. Unlike traditional GPR pushcart technology, which requires operators to perform grid marking, AUSMOS established the region of interest with minimal support from the operator. This support included reviewing the surroundings for any potential obstructions for which there were none. Where traditional GPR systems require scanning the region in multiple passes to cross perpendicular to the assets, AUSMOS made a single pass to locate the potential assets below the ground.
Moreover, due to the powerful post-processing implemented, AUSMOS has a stronger potential to compensate for misalignment between the antenna and the buried below ground infrastructure, as would be the case when there are differences between as-designed and as-built utilities. This resulted in the system’s reconstruction of assets both parallel and perpendicular to the antenna. Similar results may be seen if the asset is buried in a more substantial misalignment (e.g., 45°).
During data acquisition, AUSMOS captures data using its two onboard sensors: 1) ground penetrating radar and 2) electromagnetic sensor. This data is then processed and interpreted by the operators onsite. Once processed, the GPR data may be visualized as both a 3D point cloud and a 2D C-scan. The EM data is shown as a static field intensity plot. For the latter, as expected, no loaded high-power electrical cables were found in the region. Results shown herein are for the GPR.
Picture above: Identification of assets using ground penetrating radar in AUSMOS’s user interface.
Following scanning, this test culminated in ground marking that showed correspondence with existing land markers (trench). Since AUSMOS performs passive electromagnetic locating, assets were painted pink to represent uncertain or unknown facilities. These results showed strong agreement with the anticipated assets in the region per the survey drawings and prior trenching activities as shown below.
Picture above: Comparison of AUSMOS mapping to anticipated utilities. AUSMOS has located the assets at the following approximate depths: Asset 1: 0.75m (Foul sewer per drawing), Asset 2: 0.75m (Gas per drawing), Asset 3: 0.625m (British Telecom per drawing), Asset 4: 0.625m (British Telecom per drawing).
Picture above: Before and after site mapping.
Next Steps for AUSMOS
Following this case study, ULC Technologies will continue deployment of the robot both in the UK and US. This will focus on demonstrating the AUSMOS technology across various use-cases. For more information on AUSMOS or to discuss pilot programs contact our team.