- Why ULC?
- R&D Services
Research & Development
Leading Innovation. Driving Results.
- Industries
X-ID CROSS BORE DETECTION SERVICES
Our patented acoustic technology detects cross bores from within gas mains and services. Learn MoreLIVE GAS MAIN INSPECTION
We are leaders in the deployment of camera and crawler systems into live gas mains. Learn More
PORTABLE EMISSIONS RECOVERY
Our drawdown compressor technology helps gas distribution utilities reduce emissions. Learn More
AIM: AI-POWERED UTILITY MAPPING
Using vehicle-mounted cameras along with AI and Machine Learning to map electric distribution poles and pole-mounted assets. Learn More
CIRCUIT BREAKER RACKING ROBOT
Breaker Racking RobotAutonomous mobile robot designed to rack and unrack large breakers within substations. Learn More
ELECTRIC CONDUIT INSPECTION
Our field service teams provide video inspection of conduits prior to cable pulls to identify obstructions and pinpoint damages. Learn More
Machine Learning for Jacket Foundation Inspection
ULC used machine learning to enable more efficient inspection of jacket foundations at the Block Island Wind Farm. Learn More
Electrical Conduit Inspection Services
Our field teams provide internal inspection of conduits to pinpoint obstruction and damage prior to cable pulls. Learn More
Robotics & Technology Development
We work with leading energy companies to develop, commercialize, and deploy robotic systems and technologies that support the construction, maintenance, and inspection of infrastructure. Learn More
ROBOTIC GPR MAPPING AND MARK OUT
AUSMOS is an autonomous robotic platform that detects and marks-out below-ground infrastructure using sensors. Learn More
VEST: VACUUM EXCAVATION SOFT TOUCH
VEST improves the performance of vacuum excavation by integrating supersonic air nozzles into the vac-ex tool head. Learn More
UM-RADR: UNMANNED RAPID AIRFIELD DAMAGE REPAIR
Robotic platform is deployed to damaged airfields to remotely perform repairs. UM-RADR qualifies for Commercial Solution Opening (CSO) status. Learn More
- Products & Services
Field Services
Products
Live Gas Main Inspection Cameras
Emissions Recovery
- Company
Project Overview
After a feeder outage occurred overnight in Astoria Queens, Con Edison notified ULC Technologies in order to deploy our collaborative Automated Cable End Preparation solution in a live environment. The innovative platform was designed to address three things, enhanced safety with human-free cable preparation, improved consistency and repeatability, and time savings.
ULC operators were able to take control of the machine remotely from outside the underground cable vault, monitoring camera feeds and controls throughout the process. This field work resulted in a successful deployment of the machine leading to the completion of the world’s first fully remote end preparation of three underground cable phases with no human intervention.
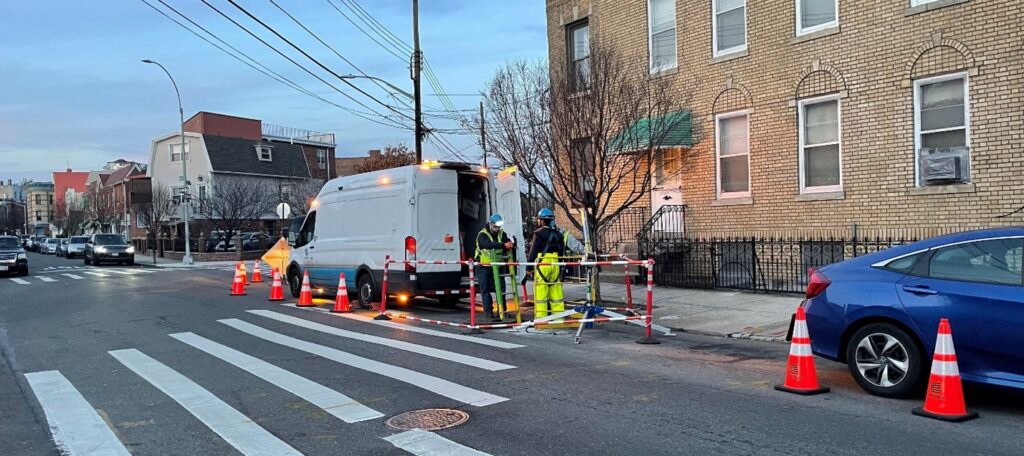
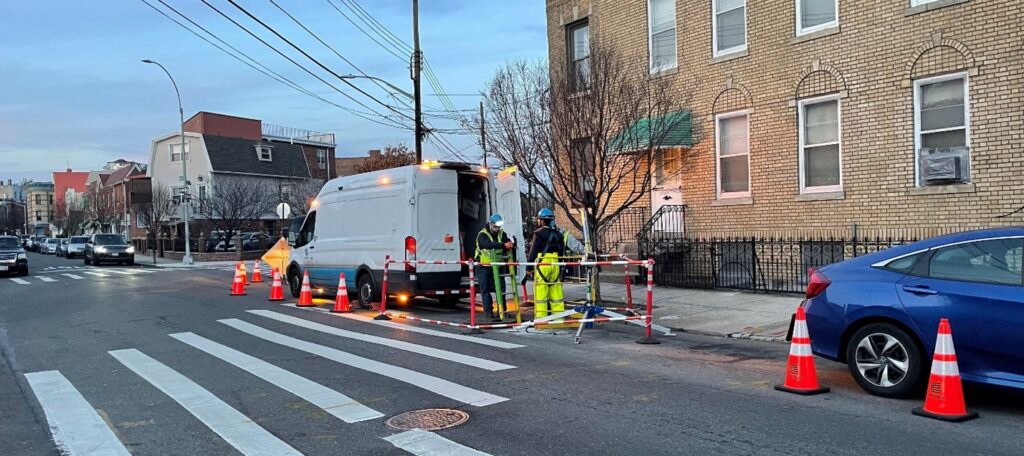
Project Details
Location: Astoria Queens, NY
Duration: 26 minutes per phase
Result: Completion of the world’s first fully remote end preparation of three underground cable phases with no human intervention
Background
In the utility and renewable energy industries, medium voltage (MV) cables are widely used to move energy in large electrical networks, from city-scale grids delivering power to consumers, to interconnecting large-scale wind and solar farms. Many medium voltage lines are buried underground and are terminated at vital points throughout a network. Installation and maintenance of interconnections for underground lines pose significant challenges to these industries and their workers. Each cable’s construction includes numerous layers, each made from different materials, with unique characteristics that each demand distinctive removal methods.
Presently, MV cable end terminations and splicing are performed fully manually by highly trained and skilled individuals in hazardous, confined settings. These workers often use basic hand tools such as straight knives to perform one or all steps of the cable end cutback process. The highly variable nature of human-executed work and variations in the cable itself create susceptibility to avoidable premature failures due to erroneous or subpar quality preparation. These failures can be extremely costly and may cause service outages or loss of work contracts.
Meanwhile, qualified operators are in short supply and frequently exposed to dangerous field conditions. This danger is amplified when completing repairs or maintenance near potentially live cable lines. The cable end preparation process should not be as difficult, expensive and risky as it is today.
More specifically, Con Edison Company of New York operates one of the world’s largest energy delivery systems as the chief supplier of electricity to consumers in the Greater New York Area. Con Edison’s mission is to provide energy to their customers safely, reliably and sustainably, and this machine is a big step forward in realizing those objectives.
Development
Day in and day out, Con Edison staff works tirelessly throughout the New York City area to ensure smooth and reliable operations. Part of this responsibility is ensuring the networks containing over 1000 feeders are operating at all times. When a feeder experiences an outage, Con Ed enters an urgency response mode to swiftly identify and de-energize the affected area, send operators to cut out the damaged sections, and install a temporary Live End Cap (LEC) allowing the remainder of the network to resume normal operation. A big challenge with this process is the need to balance speed, safety and quality under such critical conditions. In the past, there have been incidents in which operators have been exposed to live cable while in the manhole. As a result, Con Edison has adopted strict, time consuming, costly checks and procedures to be absolutely certain the targeted cable is completely dead prior to work.
Therefore, Con Edison approached ULC Technologies with this procedure in mind to develop a machine capable of performing the entire LEC installation process from beginning to end with no operators present inside the manhole. Through collaborative efforts, we have developed the Autonomous Cable End Preparation Machine, a platform capable of automating the preparation of underground MV cables for termination.
This system consists of several independent subsystems controlled through a centralized processing computer and user interface. It can be secured onto the middle of an uncut cable in the field and uses electrical actuators to provide precise coordinated motion along the axial and circumferential directions, including continuous 360-degree operation. The machine’s tool plate consists of numerous tools capable of stripping back each layer of the cable to a desired dimension using precision tool depth controls. Several auxiliary subsystems carry out additional steps such as shorting and cutting the cable. This, in combination with live camera feeds, allow an operator to successfully monitor and verify the process from beginning to end from outside the manhole with no physical human intervention.
The current generation machine is the result of three phases of R&D, resulting in a system specially designed for LEC installation, providing the following benefits compared to the traditional method:
- Inherently safe human free cable preparation
- Improved consistency and repeatability
- Time savings due to operation and reduced cable status validation processes
Deployment: Astoria Queens, NY
On the morning of February 9th, ULC Technologies was notified by Con Edison of a feeder outage in Astoria, Queens that occurred overnight and was urgently requested to deploy the machine in an underground vault to prepare the cable ends of three 27kV phases for LEC installation. Con Edison quickly began required underground structure entry preparation and procedures. Meanwhile, ULC staff explained and demonstrated to Con Ed workers the process to handle and set up the machine for the first time.
With safety procedures and situation assessments completed and communicated to ULC operators, the machine was lowered into the vault via manhole. Under ULC instruction, Con Edison operators set up the machine on the first cable phase and completed the startup process before exiting the vault.
ULC operators then took control of the machine remotely from outside the vault, monitoring camera feeds and controls throughout the process. The machine performed the following functions in accordance with the required steps to get ready for LEC installation:
- Shorting
- Cutting
- Ejection
- Ground Straps Cutting
- Jacket Cutting
- Jacket and Ground Straps Removal
- Insulation Removal
- Semiconductor Scoring
- Cable Heating
- Semiconductor Removal
Results
All 10 of these steps were successfully and fully remotely completed from outside the manhole, leaving a properly cutback cable end exposing the required amount of each cable layer to install an LEC. The LEC installation mechanism planned to be completed in future development work, and so the installation itself was completed by Con Edison staff manually. The same process was repeated two more times to complete the other two cable phases.
The result of this field work was completion of the world’s first fully remote end preparation of three underground cable phases with no human intervention. The process took on average 26 minutes per phase and can be further improved with optimization and development of standard operating procedures.